Nozzles are an important component to liquid filling machines, I know, ‘Thanks, Captain Obvious!” However, they’re often overlooked when searching for the right liquid filling solution for your production needs. They are a critical element to the success of your liquid filling – designed to control the direction of fluid flow, making for accurate fills day-after-day.
There are a large variety of nozzle offerings. Today, Ken Himes, FILAMATIC’s National Sales Manager, will be breaking down the variety of nozzles and what to be aware of when deciding what works best for your liquid filling application.
1. Straight-Through Nozzles
Straight-Through Nozzles, or open nozzles, are the most common and all-purpose nozzles you will see on most liquid filling machines in use. As the name suggests, an open nozzle is well… open, with nothing stopping fluid flow. Of course, these nozzles still help guide liquid products into containers.
Whether utilized on benchtops or monoblocs, open nozzles can come in different sizes. Typically, you will see larger nozzles used on larger pumps. Also, open nozzle assemblies can come in a variety of different diameters and lengths. Their flexibility can be used in a wide variety of applications.
2. Ball-Check Nozzles
Ball-Check Nozzles are designed with a ball at the top of the nozzle and are spring-assisted. When a liquid is going through the Ball-Check Nozzle pressure pushes the ball up so liquid can pass-through. When it stops, the ball comes back down and closes the nozzle passageway.
Depending on your application, Ball-Check Valve Nozzles or Straight-Through (Open) Nozzles will cover most production needs. It is a simple design and helps reduce dripping and control product. A screen can be added to the tip of the nozzle to control dripping and reduce foaming.
3. Valve-In-Tip Nozzles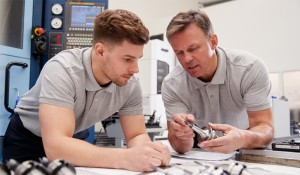
Valve-In-Tip Nozzles feature a tip at the end of the nozzle that opens and closes. This is known as a positive shutoff and is considered a “non-drip nozzle”. The shutoff occurs at either the end-of-the-nozzle or the top.
Typically, Valve-In-Tip Nozzles are used when dripping or stringing is an issue when filling. A liquid with a higher centipoise (viscosity) rating such as honey, creams, gels, lotions and hot filled products such as deodorant.
You would see Valve-In-Tip Nozzles used with gear and lobe pump systems, as well as flow meters. FILAMATIC proudly manufactures all of its Valve-In-Tip Nozzles for years.
4. Purge Nozzles
Purge Nozzles are used when a customer has an application where they need to purge the container that is going to be filled. Gasses, typically nitrogen, are used pre or post filling. A Purge Nozzle is essentially a nozzle within another nozzle. The inner nozzle fills the product into the container. The outer nozzle will send pressurized gas around the inner nozzle to purge the container.
Purge Nozzles are needed when a customer wants to eliminate air in the container, after it is capped or sealed. If you use nitrogen pre-filling, it displaces air from the container.
Purge Nozzles are most often used in pharma and biotech filling applications and products that are sensitive to oxygen or air. If air is present there could be deterioration of the liquid product.
5. One Pump, One Nozzle
FILAMATIC designs machines so that each metering system and pump has its own nozzle. One pump, one nozzle. A methodology that allows FILAMATIC to tout its accuracy and compliance within those extremely stringent industries such as pharma, diagnostic, medical and biotech.
From what FILAMATIC has seen over the years, other liquid equipment manufacturers will do one pump and squeeze multiple nozzles on a single pump. This will typically not provide good filling accuracy across all nozzles.
One pump and one nozzle practice is better for control and consistency in accurately filling liquids. Reliability, this is what FILAMATIC is known for in the liquid packaging industry and what they built their reputation on.
6. Nozzle Size
Nozzles come in a wide variety of different diameters and lengths. Typically nozzles are 3 – 12 inches long and the diameters up to 1 inch.
The nozzle size really comes down to type of product being filled, speed and rate of filling, type of container, size of the opening, etc.
7. Disposable and Reusable Nozzles
Disposable nozzles are single-use and most often made of plastic. There are also stainless steel disposable nozzles but they are not as common. People prefer disposable nozzles on single-use metering systems such as peristaltic pumps, where the tubing is also single-use.
Disposable plastics nozzles are used for corrosive or metal sensitive products. There are some companies that make disposable plastic nozzles but typically they only come in up to a ½ inch in diameter. It would hard to source larger disposable nozzles.
Reusable stainless steel nozzles are primarily what FILAMATIC uses for everything they do within this capacity. FILAMATIC utilizes corrosion resistant 316 or 316L stainless steel and they work for a majority of the filling applications.
The reason you might see people using disposable nozzles over reusable is maintenance. Disposable nozzles do not require any maintenance. Reusable nozzles do need to be cleaned and/or autoclaved at some point. The process to take apart and clean nozzles is simple.
If you have additional questions on nozzle configurations, or what may work best for your filling application, please contact us 866.258.1914 and ask for Customer Service, or simply email info@filamatic.com. We would be happy to help.