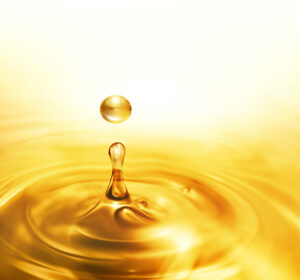
The viscosity of your liquid is essential for determining your best liquid packaging system.
Automated liquid packaging is a quick, clean, and efficient way to produce products fast. Whether you are packaging sauces, creams, gels, or water, modern flexible packaging machines have made it possible to produce these products faster than ever. However, if you are considering automating your liquid packaging, you should know a couple of things before deciding on the best machine for your application. The most crucial factor to consider for your packaging is the viscosity of your liquid product.
Understanding Viscosity
Viscosity measures a fluid’s resistance to flow, and it describes the internal friction of a moving fluid. In informal terms, it measures the liquid’s “thickness.” Thick liquids, such as molasses, have a higher viscosity and resist motion. By contrast, water or vegetable oil flows quite quickly and has a low viscosity. Viscosity is measured in centipoise (cps). Water is the standard measurement at one cps, and a product like honey has 10,000 cps. You can read more about viscosity and how to measure it here.
Why You Should Consider Product Viscosity
But why does viscosity matter for your liquid packaging system? The viscosity affects the rate at which a liquid product can travel. It affects how long it takes to set or dry and the time it takes to dispense the fluid into the packaging. The viscosity of your product will determine the type of product filler used. You will need to find a suitable filler that provides enough force to induce flow but won’t overfill the package.
How Fill Temperatures Affect Viscosity
When heated, most liquids will flow more easily. This is because, when heated, the molecules of the liquid will move faster and faster. This movement overpowers the forces binding the molecules together, which results in a more free-flowing liquid. Heat additionally decreases surface tension. But how does this affect your packaging process?
The temperature at which the liquid will be filled is critical to the configuration of the packaging line. To create the most efficient liquid packaging solution, providing an accurate fill temperature is required. Any inaccuracies can result in using equipment that isn’t suitable for your needs.
Recognizing how heat and viscosity affect the flow of your liquid product is essential for finding the best liquid packaging system. These factors can tell you the best packages to use, as well as the best machines.
Liquid Filling Machine Specialists
For over 70 years, FILAMATIC has been providing a wide range of liquid filling systems to the packaging industry. We create flexible, customized solutions for every stage of your business growth. Whether you require a single handheld filling machine, a complete turnkey fill-cap-label solution, or a fully automated, integrated filling system, we have the liquid filling experience to ensure your satisfaction is exceeded.
For more information on liquid filling, capping and labeling solutions, please call 866.258.1914 or email info@filamatic.com.