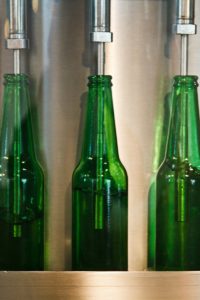
Machines with the following qualities can help maintain a consistent liquid packaging system.
A key to a successful packaging line is efficiency. If you have appealing packaging for your products and a swift packaging system, you can get your products to consumers faster and start making a profit. Of course, there are several factors to consider when you want to optimize your liquid packaging line. The following factors are going to be the most important parts of establishing a fast liquid packaging system.
The Liquid Viscosity
First, consider the viscosity of the liquid going through the filling machines and into the packages. The thickness of the liquid will help you decide which machine to use. If the wrong device is used for the wrong viscosity, it could significantly delay production and even cause a machine breakdown.
Product Traits
Manufacturers should also understand other factors of their products. Is it corrosive? Molten? If a product is corrosive, for example, the equipment must be corrosion resistant. The filling machines must be chosen to suit the product’s purpose and characteristics.
Product Challenges
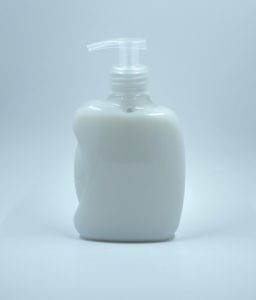
Factors like viscosity and bottle shape are important for efficient packaging systems.
Some liquid products come with unique challenges that will affect the liquid packaging system. For instance, particulates in a liquid product affect which types of pumps and seals the filling equipment requires. Then, the type of bottle or container used for the product influences the type of filler you should use. This is especially true if the bottle is an unusual shape.
Ease of Maintenance
Being able to clean your filling machines easily will also influence how fast your liquid packaging system is. Machinery that is easy to clean and easy to disassemble helps keep the necessary cleaning process efficient. This, in turn, keeps the production line running smoothly. If your machine offers a manual or auto clean in place (CIP), this will help keep cleaning smooth.
Filling Accuracy
You must make sure that your filling equipment will accurately fill, seal, and label your products. If the machine’s accuracy ratio is unpredictable, this can result in inconsistent products and lots of product waste.
Flexibility
Easy machine changeover is critical for creating a fast liquid packaging system. This means your filling equipment can accommodate many types of containers or liquids without having to change parts.
Reliable Machine Vendors
Your liquid filling machine should also come from a company that understands the filling equipment and can help you get the most out of it. A filling machine manufacturer will be able to service equipment when needed so that you avoid severe delays in the packaging line.
When used together, these factors guarantee that a liquid packaging system will maintain consistent efficiency, productivity, and profitability.
For over 70 years, FILAMATIC has provided a wide range of molten filling machines to the liquid packaging market. We create flexible, customized solutions for every stage of your business growth. Whether you require a single semi-automatic machine, a complete inline turnkey solution, or a fully-automated Monobloc system, we have the liquid filling experience to exceed your expectations.
For more information on our liquid filling machines, please call 866.258.1914 or visit – www.filamatic.com/contact-us.